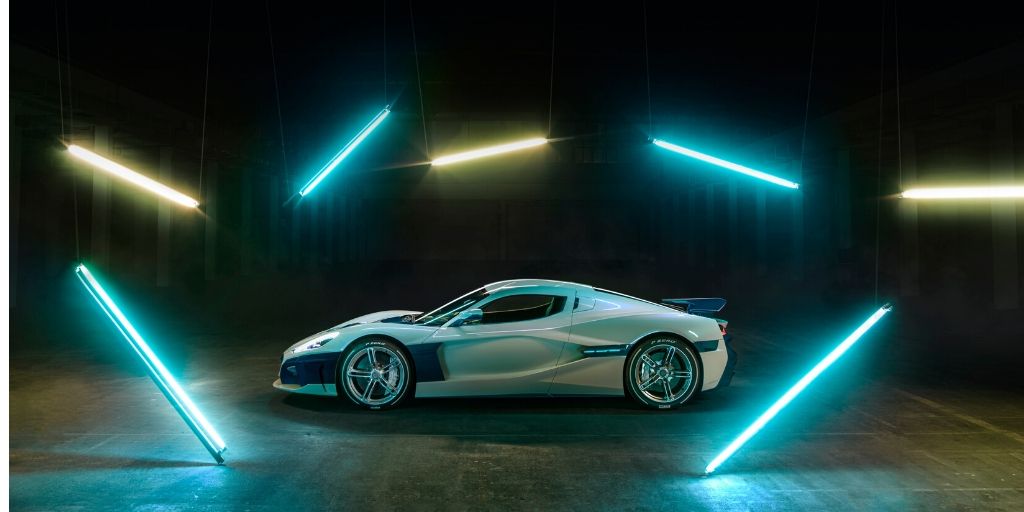
Image courtesy Rimac Automobili
In 2009, 21-year-old Mate Rimac was converting an old BMW to electric power in his garage in Croatia. Within three years, that vehicle would break several world speed records. More importantly, the project would lead to the founding of Rimac Automobili.
In just ten years since those initial tinkerings in Mate’s garage, Rimac Automobili has gone on to design two cutting-edge electric sports cars: the Concept One and the C_Two. It has also become a key supplier of electrification systems and components to such automotive icons as Aston Martin, Pininfarina, and Koenigsegg.
Rimac’s innovation and success have supercharged its growth. It has consistently doubled its staff year over year. Naturally, such breakneck expansion comes with a few growing pains — especially when one is developing technically complex large-scale systems.
Requirement Silos Led to Communication Breakdowns
When Rimac was a small company with a handful of engineers in a garage, it was easy to keep team members in the loop. Features were devised in casual conversations and developed in discussions over lunch. Requirements were recorded in Microsoft Word and Excel documents.
When Rimac grew beyond a hundred employees, however, the need for a more structured approach became obvious.
At Rimac, every system that goes into its vehicles is designed and developed in house, by small teams. Working with requirements in the relatively closed environments of Microsoft Word and Excel, Rimac’s teams began to operate in silos. They didn’t always realize how their development decisions would impact others. Consequently, their review process began to break down.
For example, a small team might decide on a change and move forward with it. Communication of that change to affected teams, however, was not always timely. And when those teams were notified, it was through emails — which often got lost in crowded inboxes.
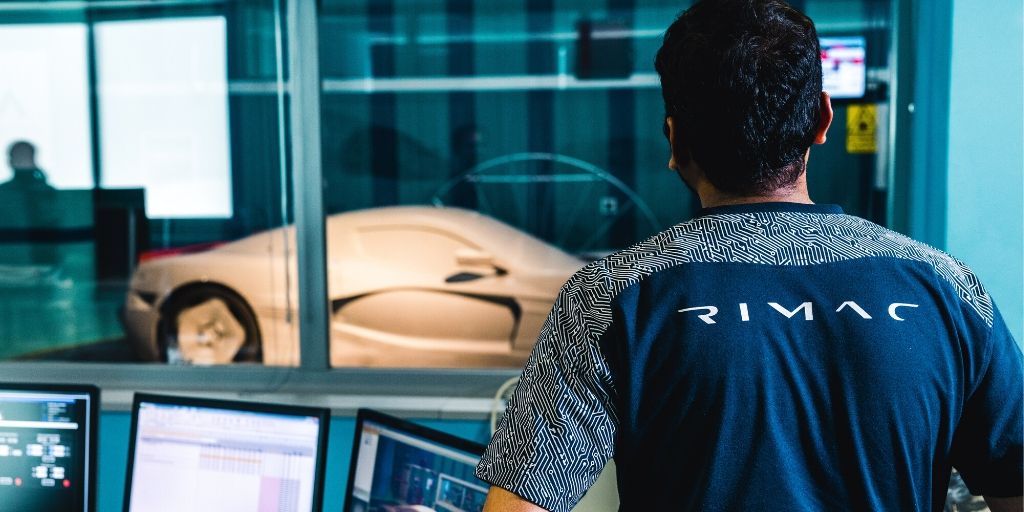
Image courtesy Rimac Automobili
Homebrewed Headaches
Eventually, Rimac tried to standardize its process and improve communication. The team started by storing requirements as numbered items in Microsoft OneNote. But as requirements were changed and others added, the numbering was altered. References in emails to specific requirements quickly went out of date, resulting in confusion and delay.
Next, Rimac developed their own requirements management tool. This homegrown solution worked a bit better than OneNote, but it was of limited utility in proving compliance with homologation standards and directives.
As an automaker, Rimac must adhere to international homologation — a vehicle approval process through which companies receive a government-issued certificate declaring their product is ready to enter the market. When Rimac’s C_Two Product Manager, Marko Šustić, asked his functional safety experts how other companies were managing compliance, they suggested Jama Connect™.
An Across-the-Board Process Upgrade with Jama Connect
Not long afterward, Rimac contacted Jama Software and set up a demonstration workshop. As Rimac’s engineers laid out their predicament, none of their issues came as a surprise to Jama’s Professional Services team.
“When we were describing the problems we were having, the Jama team members were smiling with every new problem put on the table,” Šustić says. “Because they knew Jama Connect would basically solve all of them.”
Once they began using Jama Connect in 2018, it didn’t take long for Rimac to become believers. Communication and collaboration between teams and suppliers improved rapidly. Confusion around requirements all but evaporated. Traceability and compliance issues were soon resolved as well.
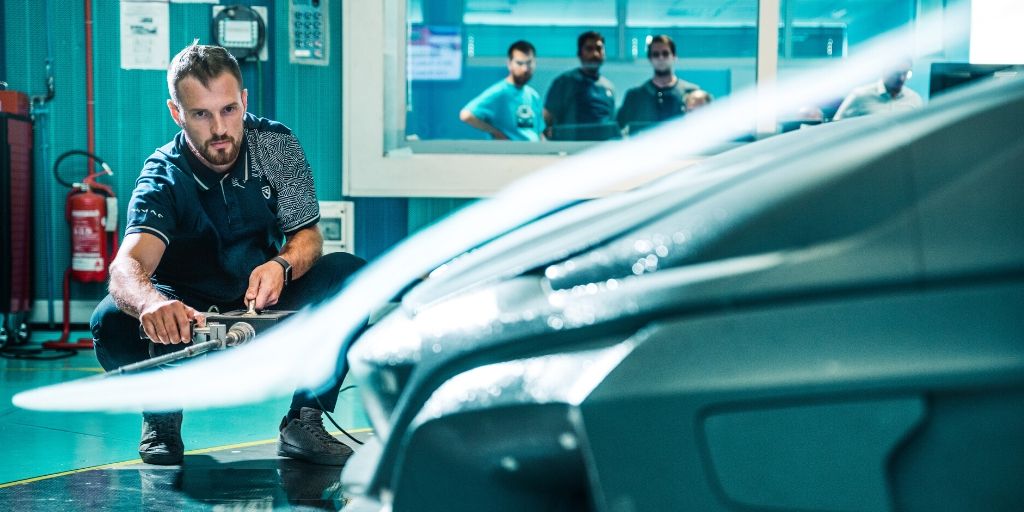
Image courtesy Rimac Automobili
Clearer Requirements
One immediate and unexpected benefit of using Jama Connect is that it has helped Rimac’s team members write better requirements.
Before adopting Jama, Rimac’s engineers tended to write their requirements in long paragraphs built from vague sentences that were confusing and prone to misinterpretation. These muddled paragraphs slowed review by the rest of the team. Plus, they were difficult to revise when sent back for correction.
Using Jama Connect, team members have learned that the long paragraphs they had been writing often harbored multiple requirements intermingled together. They’ve learned how to break those paragraphs down to their elemental components and to tag each with a unique ID that will remain unchanged throughout the system lifecycle. Rimac’s requirements have become easier to understand and review, easier to reference, and easier to implement and verify.
Simplifying Compliance with “Awesome” Traceability
Another aspect of Jama Connect that continues to impress Rimac is it’s traceability features. These help teams track requirement interdependencies throughout the development and verification chain. They’ve helped Rimac ensure compliance with applicable regulations and demonstrate that compliance to relevant authorities.
“The traceability is the wow factor,” says Šustić. “It’s awesome, because I can open up a comment that our CEO made, that I then recreated as a requirement, and from there, I can trace it all the way down to, say, a specific lightbulb.”
Smoother Collaboration with Partners
Thanks to Jama Connect, Rimac is finding it much easier to collaborate with its external partners as well.
When the team was previously sending out requirements in Word documents, miscommunication was frequent. Now, Rimac can easily collaborate with partners in on-site workshops, editing requirements directly in Jama Connect in real time. When they aren’t in the same room, it’s quick and easy to export requirements and send them to suppliers — with full confidence in their accuracy.
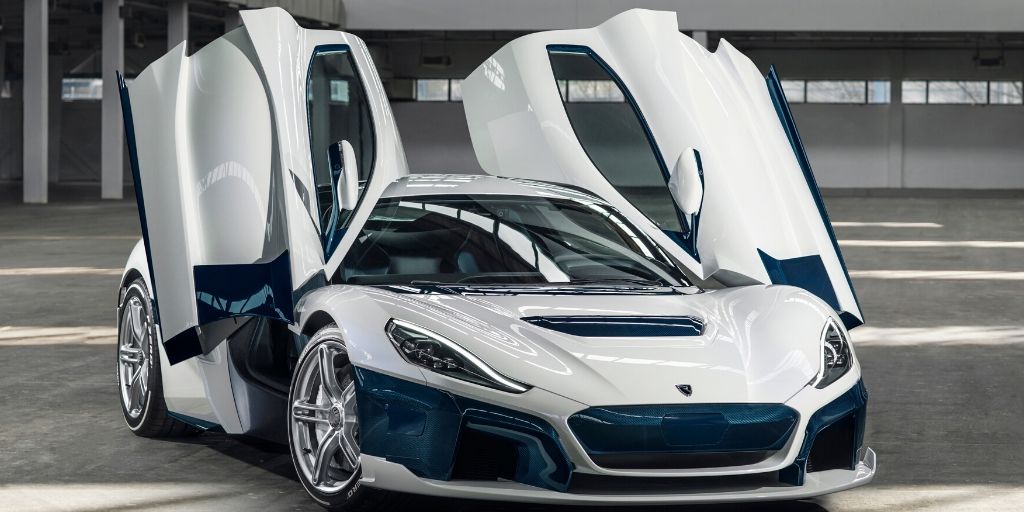
Image courtesy Rimac Automobili
Proving Functional Safety Beyond a Reasonable Doubt
Finally, by embedding compliance directly into the development process, Jama Connect takes care of most of the heavy lifting in proving functional safety. Providing compliance documentation to Rimac’s functional safety experts is no longer a hassle. There’s no scrambling to satisfy audits after the fact.
“Now, when I deal with our functional safety partners, I just give them the login credentials to Jama Connect,” Šustić says. “They can log in and type their verification and validation plans in the project. Since they’re already familiar with the software, everything works great, and it’s much more streamlined.”
The Road Ahead
Rimac continues to expand its use of Jama Connect throughout its operation. They’re especially interested in using Jama Connect to facilitate reuse of existing requirements in future vehicle development. They’re looking to further develop autonomous driving features already in use in the C_Two, for example.
Rimac’s next goal is to grow from a low-volume manufacturer of complex, high-end electrification components, to an established, high-volume tier-1 supplier for the industry. Jama Connect will be there to help them meet the challenges of greater volume, mounting complexity and increasingly stringent safety regulations.
To learn more about how Rimac is employing Jama Connect to breakthrough new boundaries in automotive development, read our customer story.